

AI Production Lines
Our state-of-the-art drip irrigation production lines are a revolutionary advancement in the industry.
Through a complete reengineering of the most sophisticated software in drip irrigation manufacturing, paired with the integration of advanced AI capabilities, we have achieved numerous industry-first innovations.
These breakthroughs deliver significant, measurable benefits across production processes, creating a set of competitive advantages:
-
Enhanced efficiency
-
Increased productivity
-
Lower production costs
-
Streamlining operations
-
Reduced maintenance costs
-
Increased components life
-
Higher return on your investment
Our technology ultimately provides greater value for your business, helping you achieve optimal performance and positioning you company ahead of the competition in a rapidly evolving market.
AI Process Engineering
Our production line technology has now reached an advanced level where it can detect deviations from optimal process parameters and dynamically auto-correct critical variables, ensuring consistent alignment with target specifications.
This innovative software continuously makes micro-adjustments to maintain precise spacing uniformity and coil length, delivering an unparalleled level of production accuracy. With these advancements, we alleviate the operator’s workload by removing the need for manual fine-tuning and eliminating guesswork and trial & error practices, allowing them to focus on productivity rather than troubleshooting. In addition, we have streamlined the process further by introducing a real-time quality control feature.
This function alerts the operator when produced coils do not meet set QC standards, freeing them to focus on other valuable tasks and enhancing operational efficiency. These improvements reflect our commitment to empowering operators, increasing productivity, and ensuring the highest quality standards in every coil produced, all while simplifying the production environment.
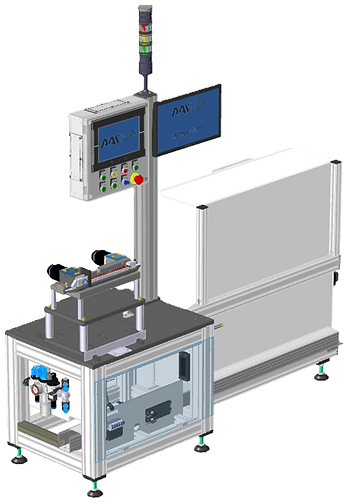
AI Speed Optimization
Intelligent Feeder Control
Our pioneering AI-driven software, combined with an advanced mechanical design, establishes a new benchmark in emitter sorting technology.
The software continuously fine-tunes feeder parameters to maintain optimal emitter throughput, ensuring a constant, uninterrupted supply of emitters to the production line. This reliability eliminates any disruption in feed, consistently meeting production demands without fail, thus, boosting reliably the production speed of the machine.
By implementing automatic adjustments, we empower operators to bypass the tedious process of manual micro-adjustments. Additionally, our “Problematic Emitter Management” feature further minimizes the need for operator intervention by detecting and addressing emitter issues in real time.
Together, these innovations substantially reduce line stoppages and scrap rates, enhancing overall efficiency and maximizing productivity. This intelligent, streamlined approach sets a new industry standard, where precision and automation align to deliver consistent quality and unmatched operational efficiency.

AI Production Augmentation
Signal Rejection
Our industry-first software introduces a groundbreaking approach to production accuracy by distinguishing between normal and abnormal production conditions in real time.
Utilizing advanced data analytics, the system continuously monitors and assesses signals from the production line. It can intelligently determine whether to accept and process a signal or reject it as erroneous, ensuring that only relevant data is acted upon.
This capability effectively filters out noise and minimizes false alerts, allowing the system to focus exclusively on genuine production needs. By eliminating the impact of misleading signals, we ensure optimal performance, reduce unnecessary line adjustments, and enhance overall production consistency.
This advanced signal rejection technology adds a new layer of precision to our production lines, empowering operators to maintain focus on core tasks without disruptions from faulty data.

Augmenting Graphs
Our new, data-driven process and analytics provide operators with instant insights into critical process parameters via intuitive graphing. With a single glance, operators can quickly assess the status of key metrics, allowing for faster decision-making. The graphical representations visually guide operators, enabling them to spot any deviations from optimal settings immediately and prompting them toward necessary mechanical adjustments.
AI Quality Control
Intelligent Drilling
The drilling unit is equipped with advanced detection capabilities that identify irregularities in problematic emitters and spacing with precision.
The unit intelligently selects and drills only the emitters that meet quality standards, ensuring that defective emitters are bypassed.
This process is performed seamlessly without compromising line speed or the mechanical integrity of the production system.
By focusing exclusively on quality-approved emitters, our drilling unit maintains optimal productivity and consistency.
This selective drilling capability not only preserves the efficiency of the production line but also enhances product quality, minimizing waste and reducing the need for recoiling, setting a new industry benchmark for precision and reliability in emitter drilling.


Problematic Emitter Management
Our innovative AI-driven software can intelligently detect increases in the percentage of defective emitters attempting to enter the production process.
When this threshold is reached, the system automatically triggers a response, diverting the affected batch into designated quarantine bins, effectively removing it from the primary production flow.
This proactive measure ensures that only high-quality emitters proceed through the line, safeguarding product integrity. By isolating defective batches early in the process, our system reduces scrap rate, ultimately enhancing overall production efficiency.
This capability demonstrates our commitment to quality assurance through intelligent automation, providing a seamless, high-performance solution.
Pinhole Detection
We have developed a state-of-the-art pinhole detection system equipped with advanced algorithms capable of identifying pinholes as they occur during production.
This system instantly notifies the operator in real time, alerting them to inspect the current coil and address potential quality issues promptly. By catching defects at the moment of occurrence, this technology prevents flawed products from advancing further down the line, ensuring a consistently high standard of output.
Beyond its application in production, the pinhole detection system plays a crucial role in material testing and selection. By accurately identifying material vulnerabilities early on, it augments the evaluation and selection of materials that meet pre-specified quality criteria.
This dual functionality not only enhances production quality but also streamlines the material selection process, resulting in a more efficient, reliable, and cost-effective production environment.

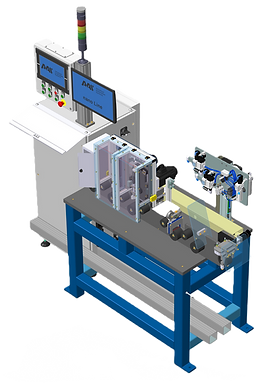

AI Proactive Shield
Proactive AI Maintenance
Our advanced AI-powered maintenance system proactively monitors all moving parts of the production line, detecting signs of both regular and irregular wear.
Operators receive immediate alerts about potential malfunctions or wear issues, enabling timely intervention before they impact performance.
This predictive maintenance capability minimizes unexpected downtime, extending equipment longevity and improving overall production efficiency.

Sensor Cleanup
The production line is equipped with intelligent sensing technology that detects dust accumulation on sensors.
When dust levels reach a threshold, the system automatically initiates a cleaning cycle, ensuring that sensors maintain optimal accuracy.
This feature helps keep equipment running smoothly, maximizing valuable production time and eliminating disruptions from sensor-related errors.
Air Turbine and Lubrication
We have developed an in-house precision smart lubrication system and a custom-engineered air turbine for the drilling unit, designed to extend component life by up to 300% and reduce maintenance costs by 80%.
The precision lubrication system ensures consistent, targeted application, reducing wear on critical parts, while the specialized air turbine optimizes drilling performance and longevity. Together, these innovations represent a transformative approach to equipment durability and cost efficiency, setting new standards for long-lasting, low-maintenance production solutions.