Buffer Technology
- A.A.S.
- Jun 14, 2022
- 2 min read
Updated: Jun 24, 2022
The buffer plays a very important role in high speed production lines since it ensures the uninterrupted supply of emitters between the feeders and the inserting unit of the line and serves as the link between them. The buffer unit of our N350 FL production line, has a total capacity of over 3.000 emitters and it is designed with two emitter lines. Its primary role is to keep the inserting rate steady with a predetermined pace, in order to avoid any production shutdown from lack of emitters.
We have developed the Smart Feeder Selection, a fully automated high precision function, which incorporates an advanced self-cleaning method of the buffer lanes. The process enables the automatic selection of the feeder that has the highest emitter quantity, in order to prevent emitter shortage in the line. Moreover, it controls the time that the emitters are buffered inside the system, while it is designed to automatically select the optimal feeding route of the emitters.
The unique Emitter Tear Protection System that our buffers incorporate, was designed and developed by our R&D department in collaboration with our emitter design team. The tear protection system eliminates emitter damage during the feeding and inserting process. Moreover, the temperature-controlled surfaces which are incorporated in our buffer, serve several important production functions which are directly linked with the final quality of the dripline.
Moreover, our buffers are equipped with an Advanced Sensing system which is able to provide several acoustic and visual alarms depending on the preset settings. This enhances the seamless operation of the production line and secures the optimum production capability.
The build quality of the buffer unit is exceptional, with all parts manufactured under strict tolerances. Moreover, the special chemical treatment of all aluminum parts ensures a trouble-free and life-time operation. All critical parts are manufactured from a special aluminum alloy, which ensures that the emitters will not be damaged during the buffering process. Finally, the high precision bearing that we use in our buffer, secures the optimum circular movement that is required. The combination of all the above guarantees that every single emitter will exit the buffer and enter the inserting unit through the conveyor, in perfect condition.
The design of the buffer allows for extremely easy, fast and problem free cleaning, resulting in minimum downtime during the overall cleaning procedure. The overall dimensions of each buffer and its emitter capacity are designed for supplying at least 3.000 Nano emitters, which translates to more than one-minute of uninterrupted emitter supply. This provides plenty of time to the line operator to react in the unlikely event of any alarm triggering.
Click here to learn more about our Production Solutions
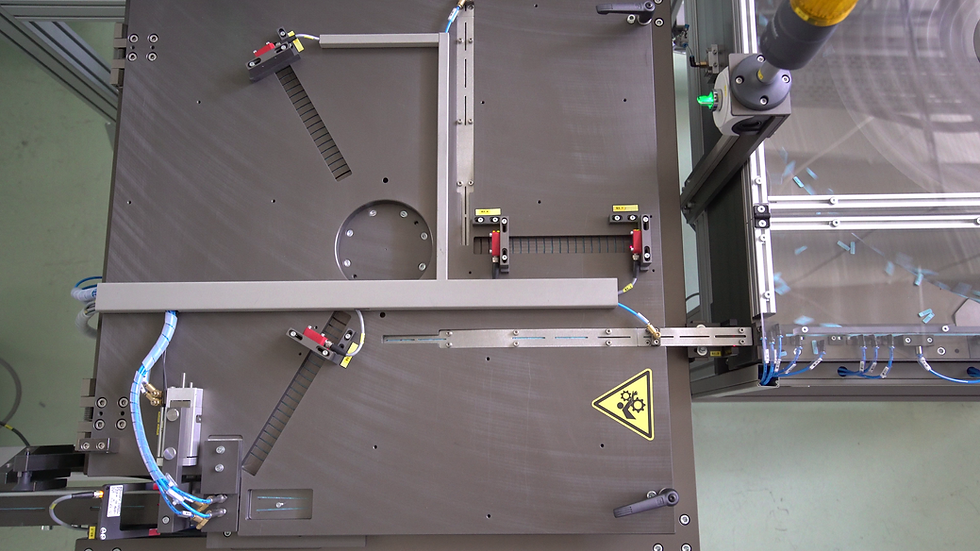
Commentaires